- ВКонтакте
- РћРТвЂВВВВВВВВнокласснРСвЂВВВВВВВВРєРСвЂВВВВВВВВ
Лазерную и плазменную резку используют для раскроя металлов,
и в ряде случаев они могут заменять друг друга. Какие это случаи, чем отличаются способы резки и какому из них отдать предпочтение?
Особенности лазерной резки
Лазерные установки состоят из трех основных частей:
- Рабочей (активной) среды – источника лазерного излучения.
- Источника энергии (системы накачки), создающего условия, при которых начинается электромагнитное излучение.
- Оптического резонатора – зеркала, усиливающего лазерное излучение.
Металл разогревается на небольшом участке. Процесс раскроя может идти при температуре расплавления или испарения металла. Второй вариант энергозатратней и применяется только для тонких материалов.
Для облегчения работы в зону резки подается газ: азот, гелий, аргон, кислород или воздух. Он необходим для удаления расплавленного металла, поддержания его горения, охлаждения прилегающей зоны, увеличения скорости и глубины резки.
Процесс лазерной резки можно посмотреть на видео ниже:
Виды лазерной резки
По типу рабочей среды лазеры бывают трех типов:
- Твердотельные. В качестве рабочего тела используется стержень из неодимового стекла, рубина или алюмо-иттриевого граната, легированного неодимом или иттербием. Источник энергии – газоразрядная лампа-вспышка или полупроводниковый лазер.
- Газовые. Рабочее тело – углекислый газ или его смесь с азотом и гелием. В зависимости от конструкции такие лазеры делятся на устройства с продольной или поперечной прокачкой и щелевые. Возбуждение газовой среды достигается с помощью электрических разрядов.
- Газодинамические. Рабочее тело – углекислый газ, нагретый до 1 000–3 000 °К (726–2 726 °С). Он возбуждается с помощью вспомогательного маломощного лазера.
Преимущества и недостатки лазерной резки
У лазерной резки есть ряд достоинств:
- благодаря отсутствию контакта с поверхностью разрезаемого металла ее используют для работы с легкодеформируемыми или хрупкими материалами;
- с ее помощью можно изготавливать детали любой конфигурации;
- экономный расход листового металла за счет более плотной раскладки на листе;
- высокая скорость и точность;
- можно резать металлы толщиной до 30 мм.
Недостатками лазерной резки считаются высокое энергопотребление, дорогое оборудование.
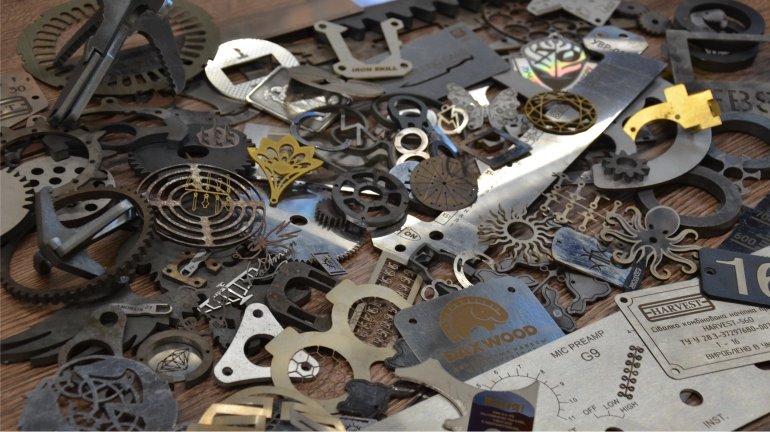
Лазерная резка оптимальна для изготовления сложных по конфигурации изделий из тонких металлов
Особенности плазменной резки
Для плазменной резки используют плазмообразующий газ: азот, кислород, смесь водорода с аргоном или сжатый воздух. В охлаждаемом плазмотроне он нагревается до температуры 5 000–30 000 °С и переходит в состояние плазмы: смеси нейтральных атомов, ионов и свободных электронов. В результате газ приобретает способность проводить электрический ток. За счет теплового расширения его объем увеличивается в 50–100 раз и он с огромной скоростью вытекает из плазмотрона. Под воздействием плазмы начинает плавиться металл.
Узнать больше о плазменной резке можно из видео ниже:
Виды плазменной резки
При использовании плазменной резки между электродом и соплом резака возникает электрическая дуга. Для этого используют источники питания постоянного тока. Дуга образуется при поднесении резака к материалу.
Различают аппараты прямого или косвенного действия. В первом случае дуга образуется между катодом плазматрона и разрезаемым материалом (плазменно-дуговая резка). Во втором – внутри резака (плазменно-струйная резка). Этот способ обработки удобен для материалов, не проводящих электрический ток.
Преимущества и недостатки плазменной резки
У плазменной резки 4 основных преимущества:
- Можно работать со сталями, алюминиевыми и медными сплавами, чугуном и прочими материалами.
- Можно изготавливать детали сложной конфигурации.
- Режет металл толщиной до 150 мм.
- Высокая точность.
К недостаткам плазменной резки относят необходимость механической обработки кромок разрезаемых материалов и конусность резов.
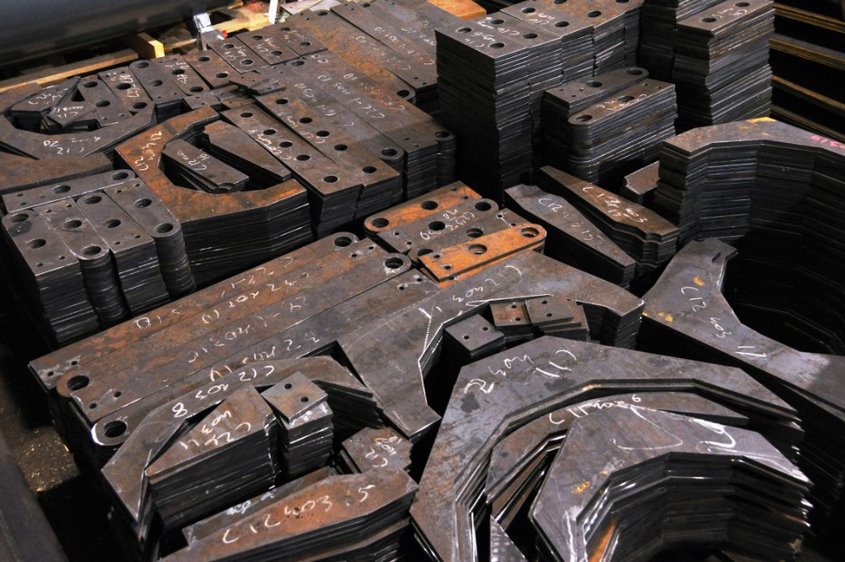
Плазменная резка чаще используется в машиностроении
Сравнение лазерной и плазменной резки
Можно выделить основные различия между лазерной и плазменной резкой.
- Толщина металла. Это основной параметр, который отличает два способа раскроя. Лазерная резка не имеет конкурентов при работе с металлами толщиной до 6 мм. При большей толщине замедляется скорость работы, и лазерную резку редко используют для раскроя металлов толщиной более 20 мм.
Плазменная резка эффективна при толщине материала 20–40 мм. Может использоваться для раскроя меди толщиной до 80 мм, чугуна – до 90 мм, алюминия и его сплавов – до 120 мм, легированных и углеродистых сталей – до 150 мм.
- Конусность реза. При лазерной резке металла толщиной более 6 мм появляется конусность кромок порядка 0,5°. По этой причине нижняя часть получаемых отверстий имеет увеличенный диаметр.
Для плазменной резки этот параметр больше – 3–10°. При выполнении отверстий этим способом их выходной диаметр меньше входного.
- Температурное воздействие. Лазерная резка характеризуется малой зоной температурного воздействия.
Плазменная резка воздействует на металлы высокой температурой, и листы толщиной до 0,5 мм могут покоробиться.
- Качество резки. По этому параметру лидер – лазерная резка. Для нее характерны стабильный и точный рез, а также отличное качество кромок.
При использовании плазменной резки образуется окалина и нужна доработка кромок.
Сравнительные характеристики обоих способов раскроя металлов приведены в таблице ниже:
Параметр |
Лазерная резка |
Плазменная резка |
Ширина реза |
Стабильна в пределах от 0,2 до 0,375 мм |
Меняется из-за нестабильности дуги в пределах от 0,8 до 1,5 мм |
Точность реза |
Высокая ± 0,05 мм |
Меняется в зависимости от износа оборудования в пределах от ± 0,1 до ± 0,5 мм |
Конусность реза |
Не более 1° при толщине металла более 6 мм |
От 3° до 10° |
Перпендикулярность реза |
Обеспечивается |
Рез сужается в нижней части, поэтому кромка плавно закругляется |
Качество кромок |
Высокое |
Нужно удалять окалину |
Температурное воздействие |
Невысокое на ограниченном участке |
Высокое. Тонкие металлы могут покоробиться |
Производительность |
Высокая для металлов не толще 6 мм. Снижается при увеличении толщины листа |
Высокая при толщине металла до 40 мм. Снижается при увеличении толщины листа |
Заключение
Лазерная резка удобнее при работе с тонколистовым металлом с большим количеством пазов сложной формы. Она позволяет получить чистые и аккуратные резы, поэтому используется для изготовления жетонов, трафаретов, указателей, табличек, декоративных элементов интерьера и деталей для электротехнических изделий.
Плазменная резка оптимальна для работы с металлом средней и большой толщины. Она уступает лазерной по качеству кромок, поэтому применяется в машиностроении или для изготовления строительных деталей и заготовок.
- ВКонтакте
- РћРТвЂВВВВВВВВнокласснРСвЂВВВВВВВВРєРСвЂВВВВВВВВ