На современных предприятиях по обработке металлоизделий, оснащенных мощными автоматизированными комплексами станков, до сих пор востребованы мастера-слесари. Они выполняют необходимые слесарные работы: холодную обработку детали, ремонт и правку конструкций ручными инструментами и на станках. Процесс слесарной работы проходит в несколько этапов.
Этап 1. Разметка детали
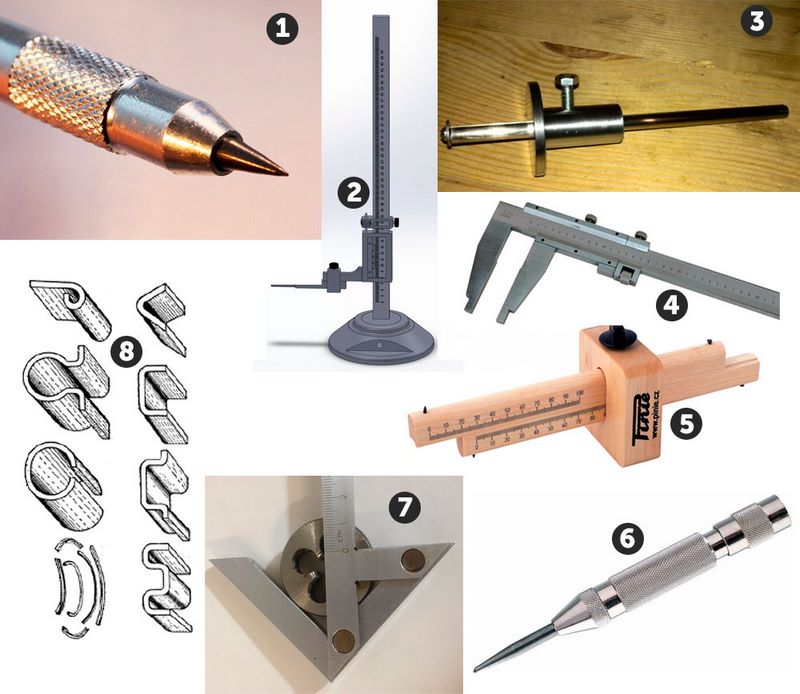
1. Чертилка. 2. Масштабный высотометр. 3. Рейсмус. 4. Штангенциркуль. 5. Штангенрейсмус. 6. Кернер. 7. Центроискатель. 8. Чугунные основы для разметки
Разметка – это нанесение на деталь определенных границ в соответствии с чертежом. Мастер размечает линии рубки, фрезеровки и расточки, а также центры для сверления.
В слесарном деле различают два типа разметки:
- Плоскостную. Делают на плоской детали, например металлическом листе.
- Пространственную. Для объемных деталей, поверхности которых расположены под разными углами относительно друг друга.
Для разметки используют инструменты:
Чертилку – стержень из закаленной стали с острыми концами для проведения тонких линий.
Рейсмус – им наносят горизонтальную разметку. Чертилку крепят на подвижном хомуте, хомут – на длинной стойке, которая установлена на круглом основании.
Штангенрейсмус – разновидность рейсмуса с массивным основанием, на которое крепится штанга с миллиметровой и микрометрической шкалой.
Разметочный циркуль и штангенциркуль для разметки окружностей. Последний нужен для точного расчерчивания окружностей с большими диаметрами.
Центроискатель для разметки торцевого центра цилиндрических заготовок. Две штанги инструмента скреплены под углом 90°, а ножка между ними делит угол пополам. Одну линию проводят по ножке, вторую – по линии краев (полок) штанг. В пересечении линий будет находиться центр торца.
Масштабный высотомер – для фиксации чертилки на нужной высоте.
Кернер – этим инструментом делают углубления на заготовке для сверления или разметки.
Приспособления для разметки – подкладки из чугуна различной формы.
На первом этапе слесарных работ поверхность заготовки тщательно зачищают и покрывают слоем мела с добавлением столярного клея или льняного масла. После того как разметочный слой высохнет, наносят разметку.
Процесс пространственной разметки по чертежу проходит в 4 этапа:
- Установка детали на чугунную разметочную поверхность.
- Нанесение основных линий.
- Нанесение вертикальных и горизонтальных линий, центров и окружностей.
- Нанесение углублений кернером.
Для плоскостной разметки используют шаблон, который накладывают на заготовку. По нему чертилкой обводят контур будущего изделия.
Этап 2. Сверление
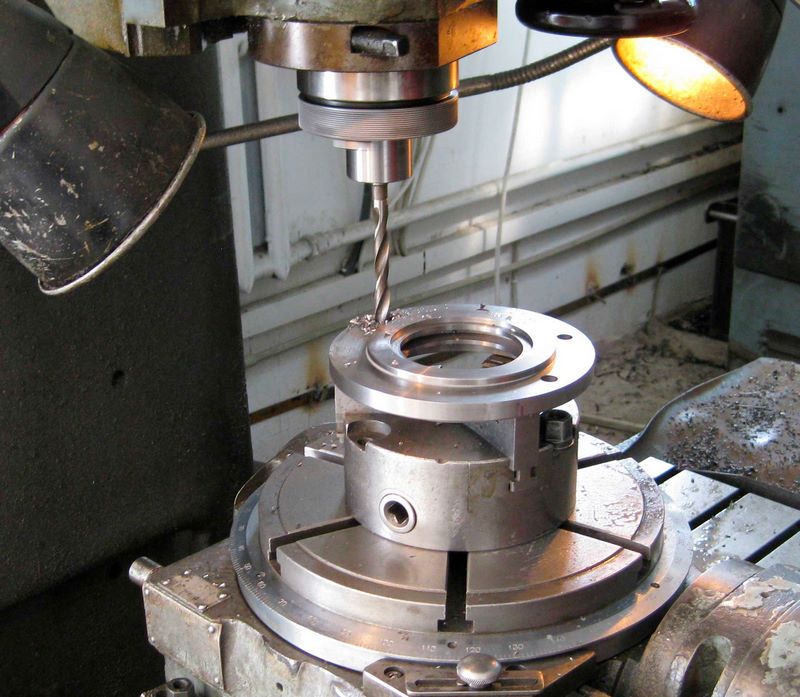
Процесс сверления необходимо продумать, исходя из задачи и материала детали
Отверстия, намеченные керном, просверливают на сверлильных станках, а также коловоротами, трещотками (для большого диаметра), ручными и электродрелями.
На этом этапе важно помнить, что от трения сверла сильно нагреваются и могут сломаться или деформироваться. Для охлаждения при сверлении стали, латуни или меди используют минеральное масло или мыльную воду, для алюминия в нее добавляют керосин. При сверлении бронзы и чугуна охлаждение не требуется.
Чтобы избежать поломки сверла на выходе из отверстия, снижают число оборотов перед окончанием сверления. Если нужно высверлить отверстие с большим диаметром, сначала используют узкое сверло, затем широкое.
Этап 3. Нарезание внутренней и внешней резьбы
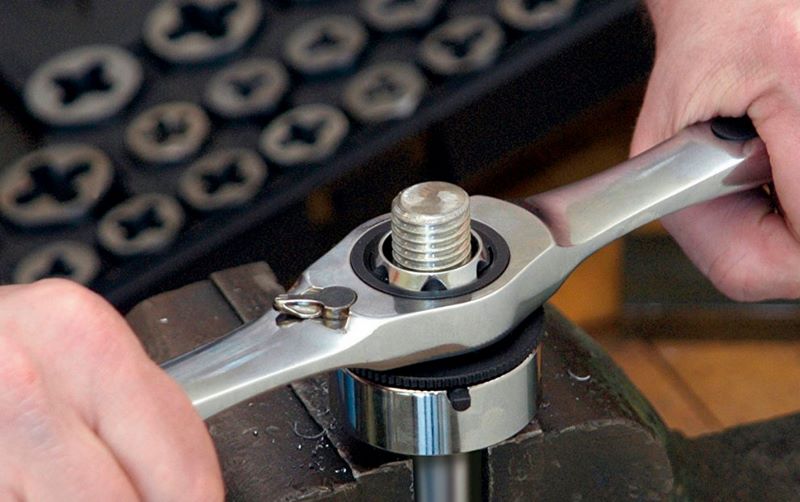
В слесарных работах чаще всего резьбу наносят вручную
Нарезание резьбы – процесс получения винтовых канавок на внутренней или внешней поверхности заготовки.
Резьба состоит из таких элементов, как:
- Профиль – форма сечения части резьбы (витка), образующаяся при полном обороте.
- Шаг – расстояние между витками.
- Высота – расстояние между крайними точками резьбы.
- Угол – определяется между двумя боковыми сторонами профиля.
- Наружный диаметр – наибольший диаметр резьбы в верхней точке.
- Средний диаметр – расстояние между двумя линиями, которые идут параллельно оси болта, на разных точках от дна резьбы до вершины витка.
- Внутренний диаметр – наименьшее расстояние между противоположными основаниями резьбы. Измеряется в направлении, перпендикулярном оси резьбы.
Различают также 3 типа профилей резьбы:
- треугольную или крепежную;
- трапецеидальную;
- прямоугольную.
Первая нарезается на гайках, болтах или шпильках для скрепления деталей между собой. Вторая и третья – на подъемниках, домкратах и винтах для передачи движения вдоль оси.
Внешнюю резьбу нарезают вручную с помощью плашек, воротков и клупп, а также на станках. Смазанную маслом деталь зажимают в тисках, на ее конец накладывают клупп с плашками, которые врезаются в заготовку на глубину 0,2–0,5 мм. Затем клупп поворачивают на 1–2 оборота вправо и влево по длине детали. На последнем этапе резьбы клупп возвращают в исходное положение, плашки врезают еще глубже и наносят окончательную нарезку.
Для нанесения внутренней резьбы используют цилиндрический или конический метчик – стальной винт с канавками для создания режущих кромок. Деталь закрепляют в тисках, а метчик помещают в вороток, который вращают по часовой стрелке с периодическим нажимом.
Этап 4. Торцевание деталей
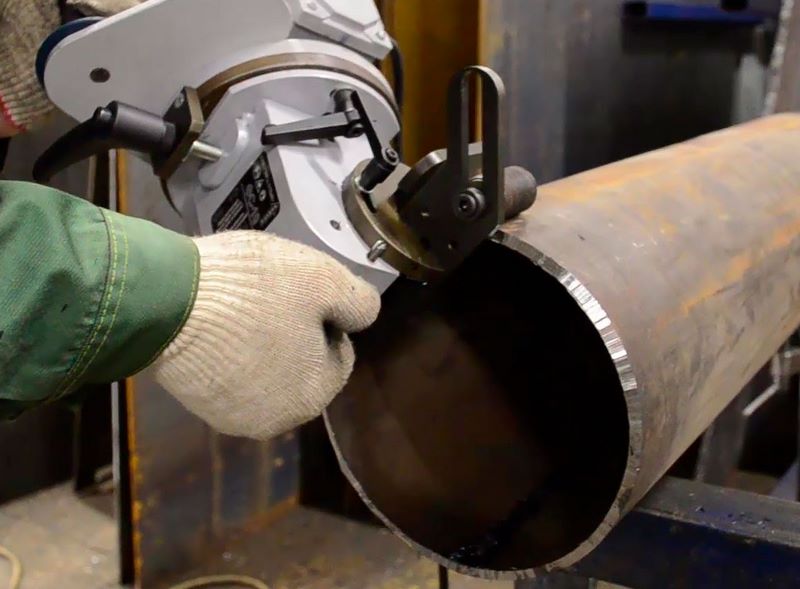
Небольшие по размеру детали удобно торцевать ручными приборами
Торцеванием называют зачистку плоскостей под фланцы, шайбы, гайки и упоры. Его проводят на специальных торцовочных станках с помощью торцевых зенкеров или с торцовочных устройств.
Торцовочные станки разделяются на:
- однопильные – заготовку вручную фиксируют на каретке и подают на пилу по одной штуке или комплектом.
- двупильные – заготовки торцуют с обоих концов по конвейерной цепи.
- многопильные – заготовки распиливают на несколько штук.
Параллельно с торцеванием на детали можно нарезать шипы и проушины.
Этап 5. Снятие фасок
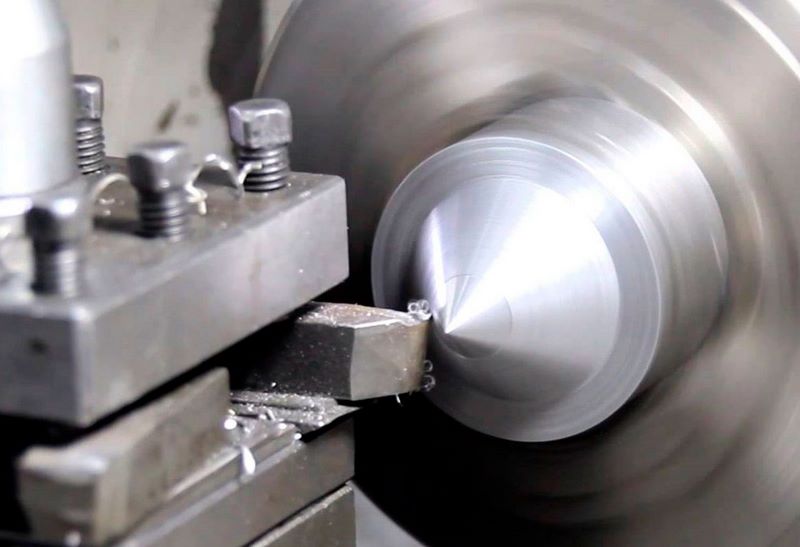
Снятие фаски необходимо, если кромку детали нужно подготовить для крепкого и надежного соединения, например для сварки
Фаска – это скос торца детали. Нарезается двумя способами:
- Термическим. С помощью газовых или плазменных резаков. Фаска получается чистой и ровной.
- Механическим. Фаску снимают кромкофрезерными машинами или фаскоснимателями.
Первый способ быстрый и недорогой, но при обработке фасок металл нагревается, что может привести к его деформации и разрушению структуры. Второй способ не оказывает на металл температурного воздействия, однако механическое снятие фаски – более трудоемкий и долгий процесс.
Этап 6. Рубка
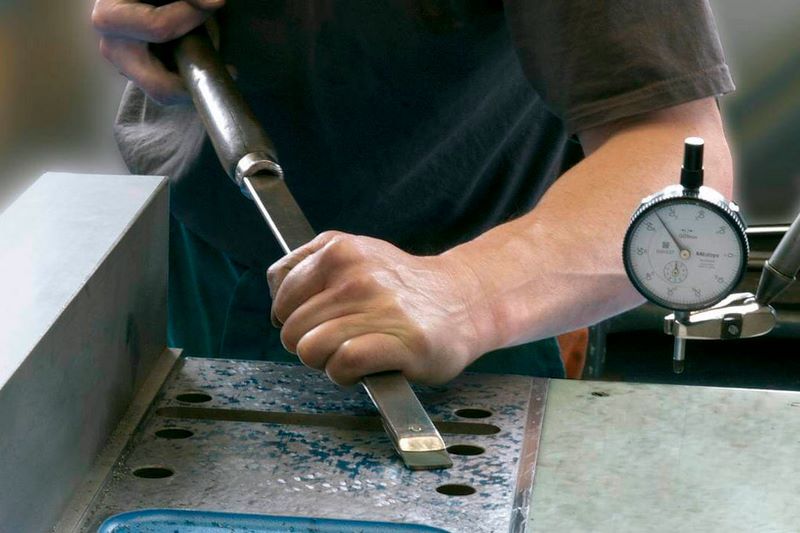
Рубка – черновой этап для подготовки детали к обработке
Данный процесс применяют для слесарных работ, где не требуется точность обработки, например для срубания выступов, пазов или грубого выравнивания. Рубку металла выполняют с помощью зубила из инструментальной стали, крейцмейселя для нанесения зарубок и ручного или пневматического молотка.
Деталь зажимают в тисках так, чтобы линия рубки проходила вровень с зажимными губками. Зубило наклоняют под углом 30–35° и ударяют по нему молотком. Если необходимо срубить толстый слой металла, рубку проводят в несколько проходов.
Если обрабатываемая деталь медная или алюминиевая, на лезвие зубила наносят мыльную воду или масло. Такие хрупкие металлы, как чугун, бронза, выкрашиваются при рубке, поэтому сначала на ребра детали наносят фаски, облегчающие проход зубила.
Этап 7. Резка
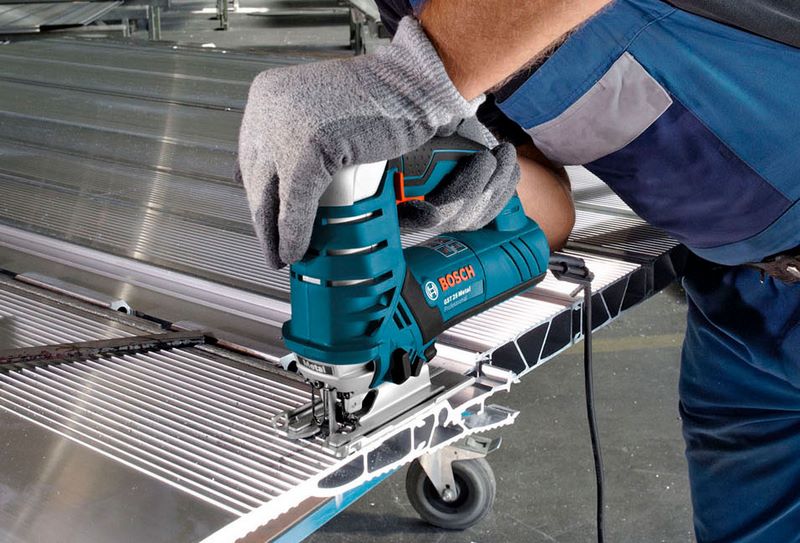
На современном производстве механические ножи и пилы для резки используются все реже. Гораздо быстрее и эффективнее резать металл электроинструментами
На данном этапе слесарь использует специальные инструменты по металлу в зависимости от структуры, толщины и размера детали.
Листовой металл чаще всего режут ручными, электрическими, гильотинными или дисковыми ножницами по разметочной линии. Небольшие заготовки режут ножовками. Резать металл вручную довольно утомительно, поэтому мастера предпочитают использовать электрические модификации инструментов, ускоряющие процесс.
Для резки труб используют труборез. Это рукоять, на которую крепится скоба с тремя дисковыми резцами. Труборез надевают на деталь, сжимают резцы и, вращая, разрезают ее. Еще трубы разрезают ленточными или дисковыми пилами.
Этап 8: Правка металла
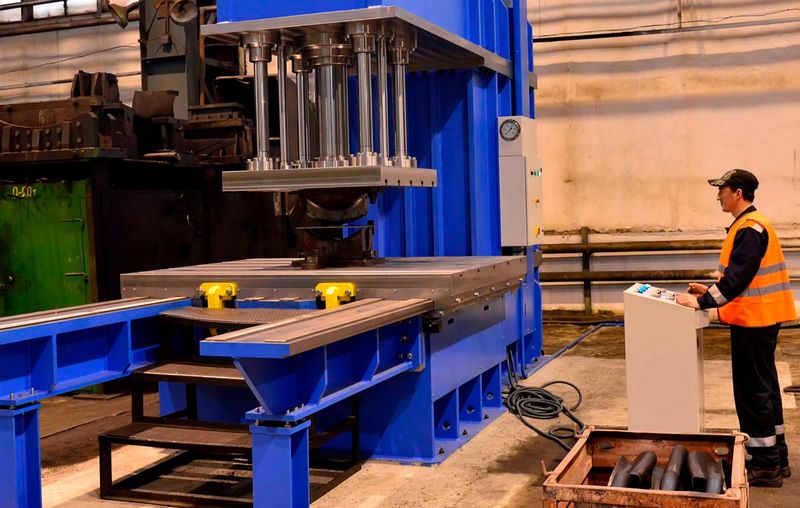
Финальную правку проще всего проводить с помощью автоматизированного пресса, который максимально чисто уберет все неровности с детали
На этом этапе мастер исправляет вмятины, выбоины, царапины, искривления и прочие дефекты на детали. Правку проводят на нагретом и холодном металле ручным или машинным способом.
Ручную правку делают на наковальне или массивной правильной плите из чугуна или стали. Основным инструментом для ручной правки небольших фигурных деталей является правильный молоток с гладким круглым бойком из меди, свинца или дерева. Листовой металл правят с помощью гладилок.
Этапы ручной правки:
- Деталь кладут на плиту и визуально определяют зазоры между двумя поверхностями.
- Видимые дефекты отмечают мелом.
- Молотком исправляют неровности, соизмеряя силу ударов: снижая силу удара при переходе от большого изгиба к малому.
Машинную правку применяют для листовых деталей или труб с помощью пресса или правильного вальца.
Для работы винтового пресса нужны два мастера: один ставит заготовку и контролирует процесс ее правки, второй вращает маховик пресса. Для работы на электропрессе достаточно одного человека.
Гибочные вальцы – это ручные или приводные агрегаты с тремя валками. Два валка расположены один над другим, их расстояние регулируется в зависимости от толщины металла. Третий валок размещается за первыми двумя и служит для более тщательной обработки. Вальцы с ручным приводом применяют для правки металла толщиной до 3 мм, а приводные – до 4 мм.
Контроль качества при выполнении слесарных работ
Главный критерий оценки качества слесарных работ – это точность изделия – соответствие размеров и форм детали исходным данным в чертеже. Конечно, абсолютного соответствия при ручной слесарной обработке добиться сложно. Это достигается при доводке изделия.
Чтобы готовое изделие получилось абсолютно точным, необходимо сверять параметры в процесс работы. Для этого используют специальные измерительные приборы, шаблоны и эталоны. В зависимости от того, какие измерительные средства применяются, методы измерения делятся на:
- абсолютный – определяют значения всей измеряемой величины, когда совпадают нулевые точки прибора и готового изделия;
- относительный – определяют отклонения точности от заданного образца, когда нулевая точка инструмента настраивается на определенный размер.
Снимают параметры двумя способами: контактным – когда измерительный прибор соприкасается с измеряемой деталью, и с помощью проекций и лазеров.